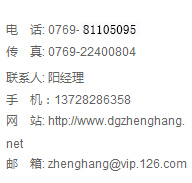
一、微弧氧化陶瓷膜的外观检验
本实验条件各种参数下所制得的微弧氧化陶瓷层外观大部分为白色,有少量试样处理后表面颜色偏向灰白色,同一试样各处颜色均匀。微弧氧化后试样表面无明显的深孔出现,外观等级分数均在70以上。试样制备过程中,我们分别对重熔后的电弧喷涂铝层采用不同型号的砂纸打磨,以获得不同表面粗糙度的原始试样表面(最光洁表面打磨止800#砂纸)。
微弧氧化后发现,几乎所有的试样的表面粗糙度都增大了,而且同等处理参数条件下原先粗糙度较小的试样处理后表面粗糙度增大反而显著,我们推测其具体原因与陶瓷层生长过程的特点有关,具体分析见本文的讨论部分。电参数对微弧氧化陶瓷层表面粗糙度的影响也较为明显。同等的前处理状态下,随着电流密度和处理时间的增加,微弧氧化陶瓷层的表面粗糙度呈增大的趋势。图4-20显示的是微弧氧化过程中试样表面粗糙度的变化情况,从1001#到1006#的电流密度为15 A/dm2,处理时间分别为:45 s,10 min,15 min,20 min,25 min,35 min。
实验还发现,如果长时间在大电流密度条件下对试样进行微弧氧化处理,将会使表面陶瓷层发生局部剥落,出现小坑。我们认为,这是由于微区内长时间能量输入过大使微熔区发生小范围“飞溅”,而且过大能量的输入使表面陶瓷层出现严重的击穿破坏。实验中这是应该极力加以避免的。
二、微弧氧化陶瓷层的耐蚀性能
从图4-21中可以看出,在各种浓度的NACL溶液中,微弧陶瓷化处理后的试样的耐蚀性能最为优良,优于重熔前后的没有经过此处理的试样,而重熔后试样的耐腐蚀性又好于未经过重熔的试样。三种材料的腐蚀增重具有相同的特点,即随着NACL溶液的浓度增加,腐蚀增重先增后减,在NACL溶液的浓度大约为10%的时候腐蚀增重达到最大。
本实验所用浸泡液中含有Cl-,溶液中又有溶解氧存在,Cl-的存在破坏了铝表面的钝化膜,或阻碍了铝表面氧的吸附而形成蚀孔,蚀孔内铝就发生溶解。在NaCl溶液中,阴极反应为吸氧反应,孔内氧浓度下降,而蚀孔外富氧形成氧浓差电池。孔内Al3+的不断增加,为保持电中性,蚀孔外阴离子(Cl-)向孔内迁移,孔内氯离子浓度升高。又因为孔内铝离子浓度升高并发生水解生成Al(OH)3和H+,这使孔内溶液氢离子浓度升高,pH值降低。孔内酸化,使蚀孔内金属处于HCl介质中,即处于活化溶解状态;而蚀孔外的金属处于富氧的中性介质中,表面维持钝态。从而构成了活化(孔内)-钝化(孔外)腐蚀电池,促使蚀孔内金属不断溶解,蚀孔外表面发生氧的还原。这样使腐蚀以自催化的过程发展下去,从而促进腐蚀破坏的迅速发展。微弧氧化层的耐NaCl溶液的腐蚀性之所以好于重熔前后的电弧喷涂铝层,是因为它的表面绝大部分为陶瓷层所覆盖。由于铝在NaCl溶液中腐蚀的阴极反应为吸氧腐蚀,而氧的溶解度又随溶液浓度的增加而减小,因此当NaCl浓度较低时(<10%),不影响溶液中的溶氧量,阴极反应不受限制,此时Cl-的破坏作用控制腐蚀的速度,因而腐蚀速度随溶液中Cl-的增加而增大。但当溶液浓度较高时(>10%),溶液中的溶氧量下降,溶氧的减少,使阴极反应受到限制,尽管这时溶液中有足够多的Cl-,但它已不是起控制作用的因素了,此时,氧的溶解量决定了整个腐蚀反应的速度。这就是腐蚀增重在10%NaCl溶液中出现极大值的原因。我们又测定了重熔电弧喷涂铝层微弧氧化前后的腐蚀极化曲线,如图4-22所示。
从图4-22中可以看出微弧氧化试样的自然腐蚀电位约-200 mV,而未微弧氧化试样的自然腐蚀电位约为-370 mV。由于自然腐蚀电位越低越易腐蚀,而未微弧氧化试样相对微弧氧化试样来说自然腐蚀电位较负,故耐腐蚀性能不如微弧氧化试样,这与前面的浸泡实验结果是一致的。
三、微弧氧化陶瓷层的耐磨性能
将微弧氧化陶瓷层的耐磨性与45钢(经840℃淬火+150℃低温回火)进行比较,得出的实验结果如图4-23所示。
由图4-23可以看出,在较短的摩擦延长米(<20 M)和较长的摩擦延长米(>20 M)情况下微弧氧化陶瓷层的耐磨性和45钢呈现出不同的优劣性:当摩擦行程相对较小时,微弧氧化陶瓷层的磨损失重比45钢稍大;而随着行程的增加,微弧氧化陶瓷层良好的耐磨损性能逐渐体现出来,尤其是当摩擦延长米达到50~60 M的时候,微弧氧化陶瓷层的磨损失重仅为45钢的1/2。我们认为,微弧氧化陶瓷层内外不同的结构和相组成是造成陶瓷层和45钢耐磨性的优劣在大小摩擦延长米条件下有所变化的原因。根据前面所做的微弧氧化陶瓷层相分析以及形貌观察我们知道,微弧氧化陶瓷层外层是较为疏松的组织,因此容易被磨损掉;而随着疏松外层的消失,陶瓷层内部的致密层显露出来,内部组织的Α-AL2O3比外部要多,其良好的耐磨性逐渐体现出来。
因此我们认为,对于精密配合的磨损件采用微弧氧化处理后可先行打磨掉外部疏松层,以避免出现因磨损初期较大失重而造成零件失效。图4-24为陶瓷层磨损前后的表面形貌。C点为较深的放电孔在磨损后的形貌,D点处为“山坡”之间的“沟渠”在磨损后的形貌,综合比较A、B、C三处形貌,我们可以推测放电孔是一种倒立的锥形结构。在图4-24中还可以可以看到陶瓷层表面的一些“沟渠”和残留小孔,在摩擦副中这些“沟渠”和残留小孔可以作为润滑油的有效载体,来减少润滑摩擦条件下的摩擦系数。
四、复合膜层的抗热冲击性能
文献提到,微弧氧化陶瓷层可在300℃水淬35次无变化。我们采用了更为苛刻的实验条件,即把保温温度提高到450℃。实验中,我们分别采用水冷热冲击和空冷热冲击的方法来进行检测。
(1)空冷热冲击
与上述方法类似,把试样放入电阻炉中加热至450℃保温5 min后取出空冷3 min,认为试样己足够冷却后,再次放入电阻炉中加热,如此反复40次后观察膜层表面形貌。
(2)水冷热冲击
把试样放入电阻炉中加热至450℃,保温5 min后取出放入水中,l min后将试样取出放入电阻炉中加热,如此反复40次后观察膜层表面形貌。与未进行此实验的试样相比较,热冲击后的试样表面几乎没有发生任何变化。可以看出,一类裂纹产生在放电孔较为密集区域,裂纹沿着放电孔的方向发展,将放电孔连接起来;另一类裂纹发生在较大的“山坡体”上。为了观察膜层在更恶劣的热冲击条件下的变化,我们对进行完实验(1)和实验(2)的平行试样又进行了一次450℃保温10 MIN加强实验,然后分别空冷和水冷至室温,图4-27和图4-28分别是进行完上述空冷和水冷热冲击加强实验后陶瓷层的表面形貌。
可以看出,膜仍然没有脱落的痕迹,只发现空冷热冲击试样表面开始出现微小裂纹,而水冷热冲击试样表面的裂纹略有所变宽。而且从试样的截面观察来看,没有发现贯穿至膜层深处的裂纹。这表明上述裂纹仅存在于膜层表面及疏松层,而对整体膜层损害不大。上述实验结果表明,复合膜层抗热冲击性能良好。与原始试样相比,热冲击后的试样没有发现特征性的变化,仅仅在表面层出现了微裂纹。由此可以推测,膜层与基体之间具有比较接近的热胀匹配。我们认为对试样处理过程中由于冶金结合而形成的的材料梯度过渡是形成膜层与基体之间具有比较接近的热胀匹配的主要原因。(正航仪器整理)http://www.zhenghangsy.net