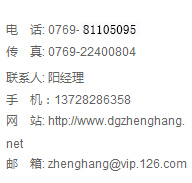
再制造是中国发展循环经济的必要途径之一,研究再制造关键技术及基础理论,对再制造产业的兴起和发展有着重要的意义。本文编者主要围绕再制造零件疲劳寿命预测及可再制造性两个方面主要进行了以下工作:
1、提出了再制造零件疲劳寿命评估方法,发展了基于有限元的疲劳寿命预测模型。即通过标准试样拉伸、疲劳试验以及估算获得材料特性;通过几何建模、动态仿真获得载荷;通过有限元分析获得局部应力;最后将获得的材料特性、载荷和局部应力代入相应的疲劳损伤模型,便可以预测再制造零件的疲劳寿命。
2、对曲轴进行了动态仿真,动力学仿真模型在ADAMS的ENGINE模块中建立。它将曲轴剖分为六个曲柄构件,然后限制构件之间的相对运动自由度,这样就避免了解静不定结构;同时用线性弹簧来模拟主轴颈处的约束。该模型不仅考虑了曲轴上作用的弯矩、扭矩及支承的弹性,而且还考虑了多缸连续点火时的相互影响,故是目前比较准确的计算模型。
3、建立了考虑弹性支撑及相邻曲拐相互影响曲轴有限元模型,得出多个工况下曲轴的应力分布。
4、对曲轴材料48MnV及其具有3Cr13电弧喷涂涂层的疲劳行为进行了研究,根据试验结果提出一个电弧喷涂修复再制造后曲轴寿命预测修正系数。
5、对发动机曲轴再制造前后的寿命进行了估算。
6、在产品可装配性评估方法和模型的基础上发展了产品可再制造性评价的模型,模型包括技术性、环境性和经济性三大模块。通过对某型发动机可再制造性的评价验证了该模型的有效性和实用性。(正航仪器编写)http://www.zhenghangsy.net